Powder Coating Machine Buying Guide: Avoid These 7 Costly Mistakes When Selecting Equipment
Correctly selecting a powder coating machine can not only improve production efficiency, but is also the key to achieving long-term cost reduction and efficiency improvement. However, companies often overlook key details when purchasing, which may lead to problems such as premature aging of equipment, rising maintenance costs, or insufficient production capacity. This article analyzes seven common cognitive misunderstandings in the industry and combines cutting-edge technical solutions to provide decision-making references for companies.
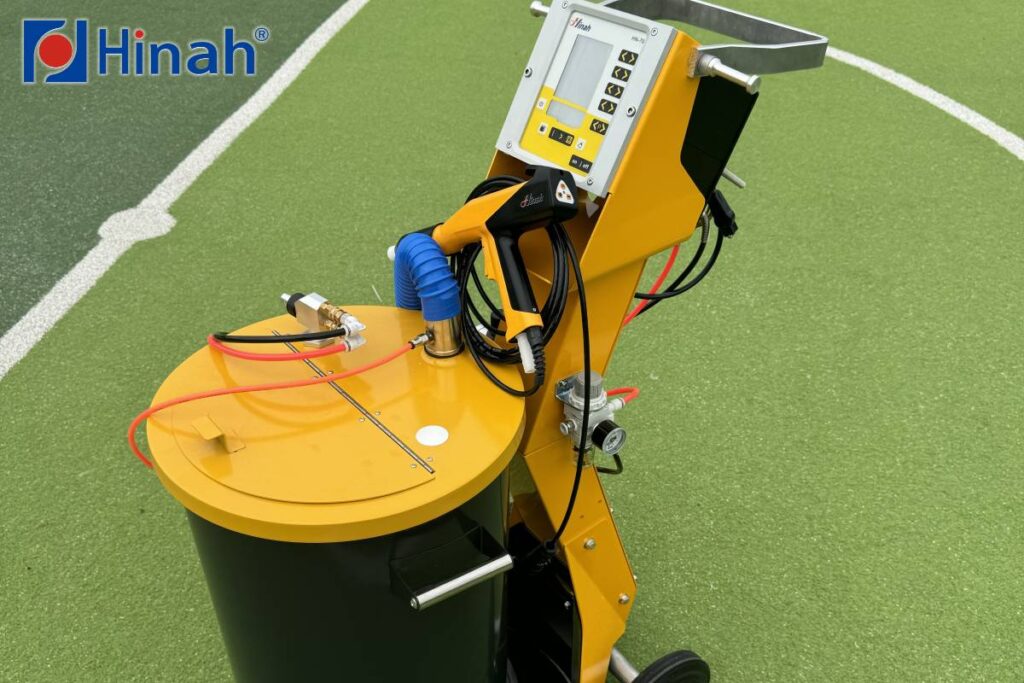
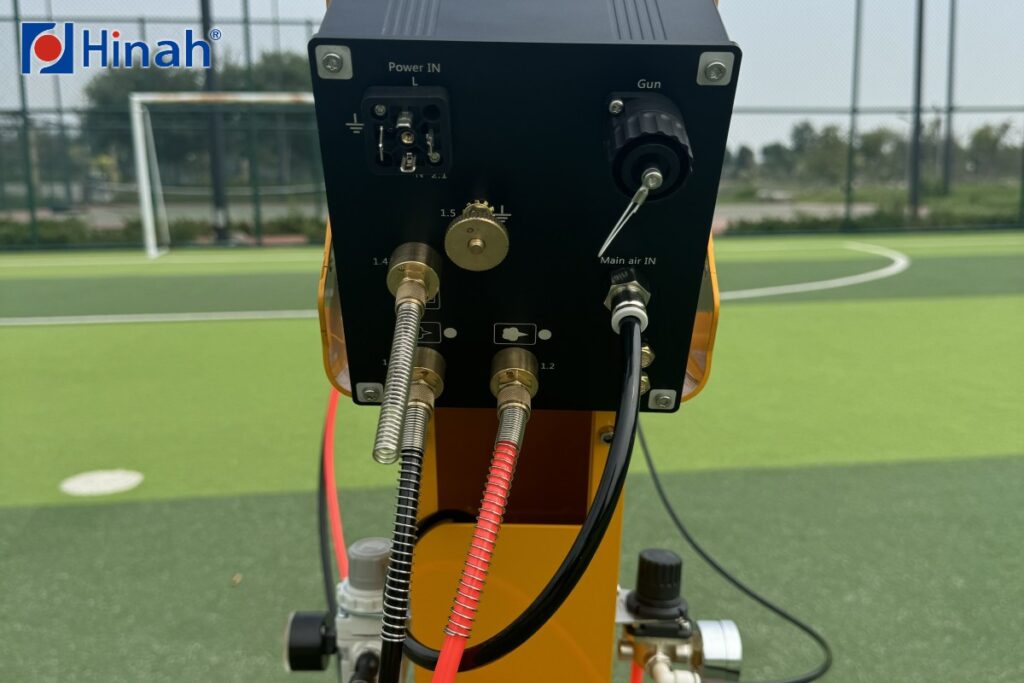
Misconception 1: Ignoring the actual considerations of production needs
When purchasing the powder coating machine, many companies often ignore the specific conditions of their own production needs and choose equipment that is too large or too small. Oversized equipment may lead to unnecessary high investment and waste, especially in the case of small production scale. While undersized equipment may not be able to meet daily production needs, causing frequent production bottlenecks and affecting overall production efficiency. Therefore, it is crucial to choose the right powder coating machine model.
Misconception 2: Underestimating the long-term maintenance cost of powder coating machine
As a high-precision equipment, powder coating machine requires long-term maintenance and upkeep. If these maintenance costs are ignored, companies may face high repair costs or downtime in later operations, which will affect production efficiency and profits. For example, regular cleaning of spray guns, inspection of electronic control systems, and replacement of some parts of coating powder spraying equipment are all necessary expenses to maintain the normal operation of the equipment. Over-reliance on low-cost equipment may lead to frequent maintenance work, which in turn increases unnecessary expenses.
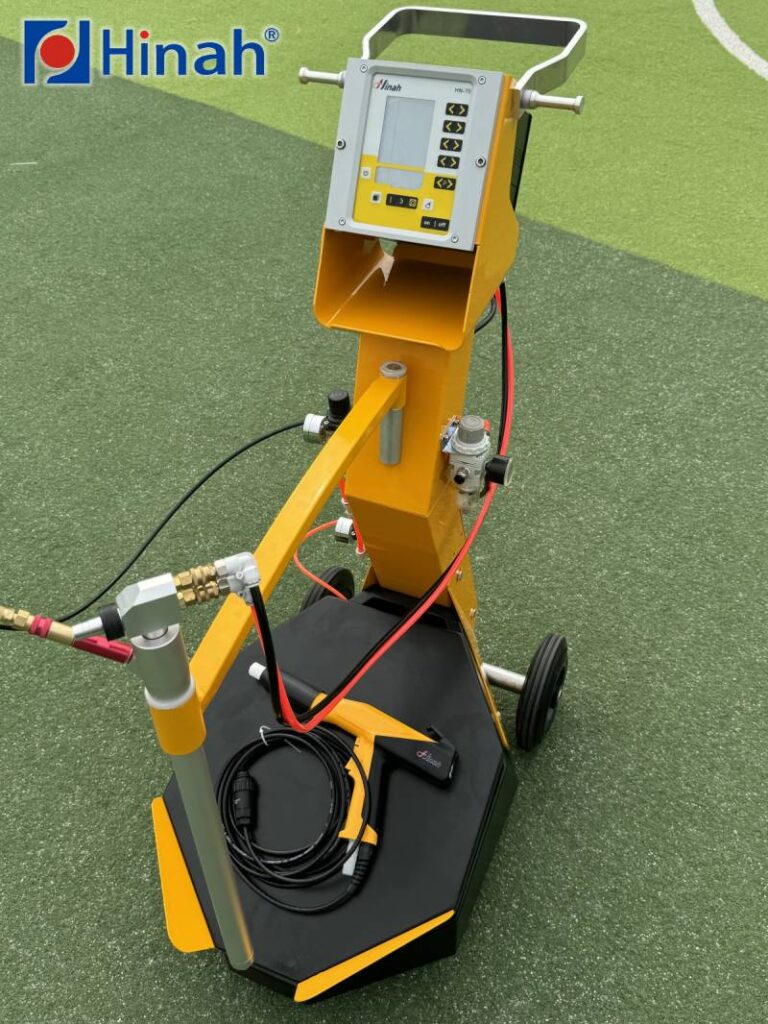
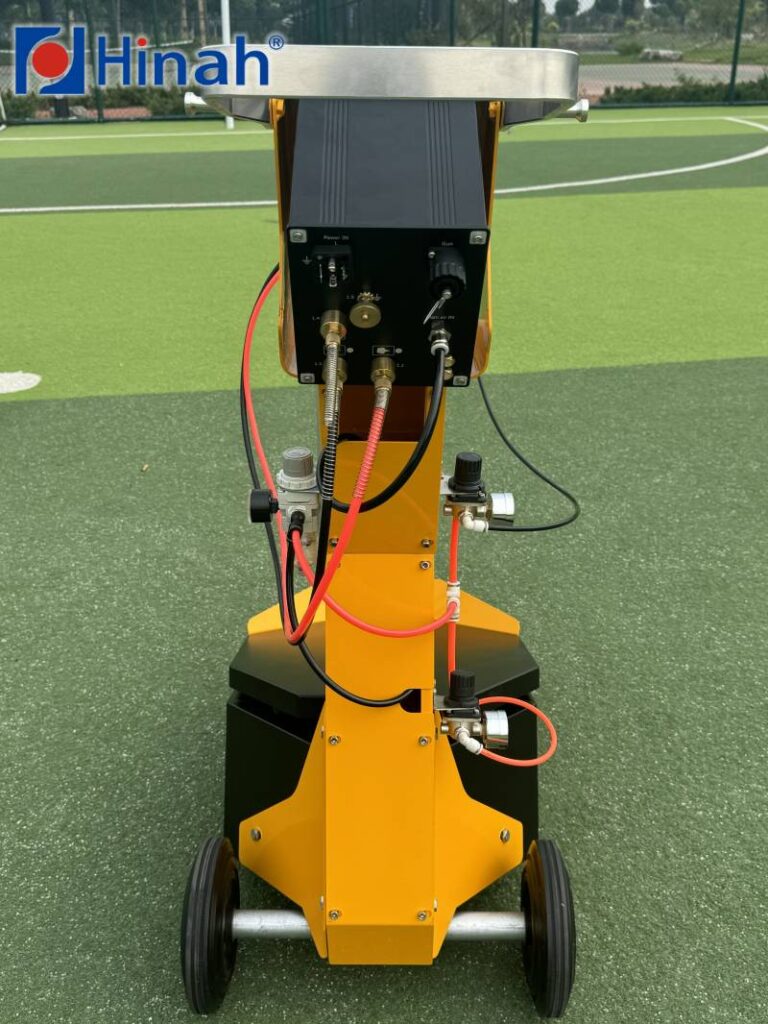
Misconception 3: Ignoring the energy efficiency of powder coating machine
The energy consumption of powder coating machines directly affects the operating costs of enterprises, especially in production environments with long-term and high-frequency operation. Many enterprises pay too much attention to the initial price of the equipment when purchasing, but ignore the energy consumption of the equipment. High-energy-consuming powder coating machines not only increase monthly electricity bills, but may also cause unstable equipment operation, thereby increasing maintenance frequency and costs.
Misconception 4: Not considering future upgrades and scalability
As market demand changes and production scale expands, the original equipment may not be able to meet higher production requirements, resulting in the equipment being unable to adapt to new production processes or process requirements. Choosing a device that is not scalable may require expensive equipment replacement or large-scale upgrades in a few years, which will not only increase additional capital expenditures, but also interrupt the normal operation of the production line. Therefore, when choosing equipment, companies should take into account possible changes in production demand in the future to avoid high costs in the later stage due to equipment limitations.
Misconception 5: Failure to evaluate the ease of operation of the powder coating machine
When purchasing a powder coating machine, many companies often ignore the ease of operation of the equipment and pay too much attention to the degree of automation of the equipment. Although automated powder coating machines can improve production efficiency, if the operating interface is complex and the settings are cumbersome, more training and maintenance costs may be required. On the other hand, although equipment that relies too much on manual operation has a lower initial investment, it is easily affected by human factors during the production process, resulting in low efficiency and unstable coating quality. Therefore, finding a powder coating machine that can find a balance between automation and manual operation is the key to improving production efficiency.
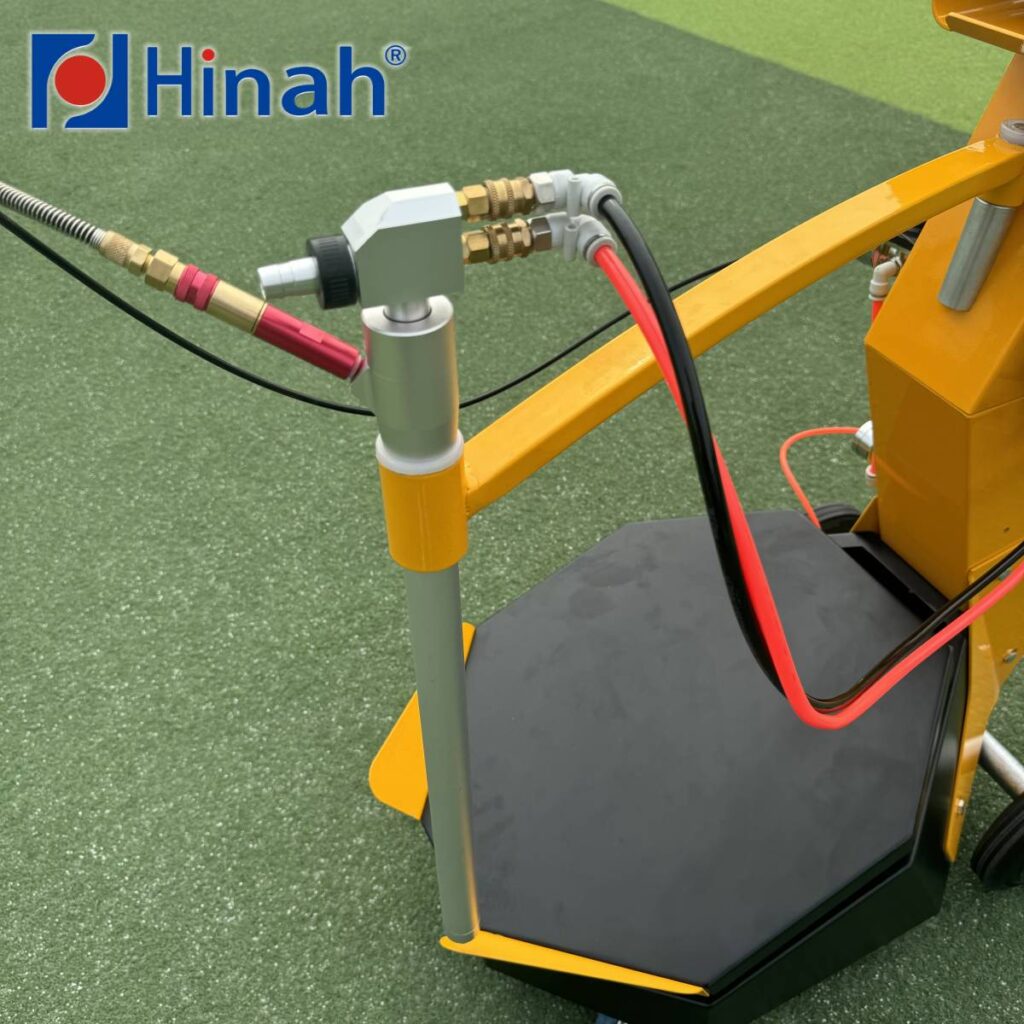
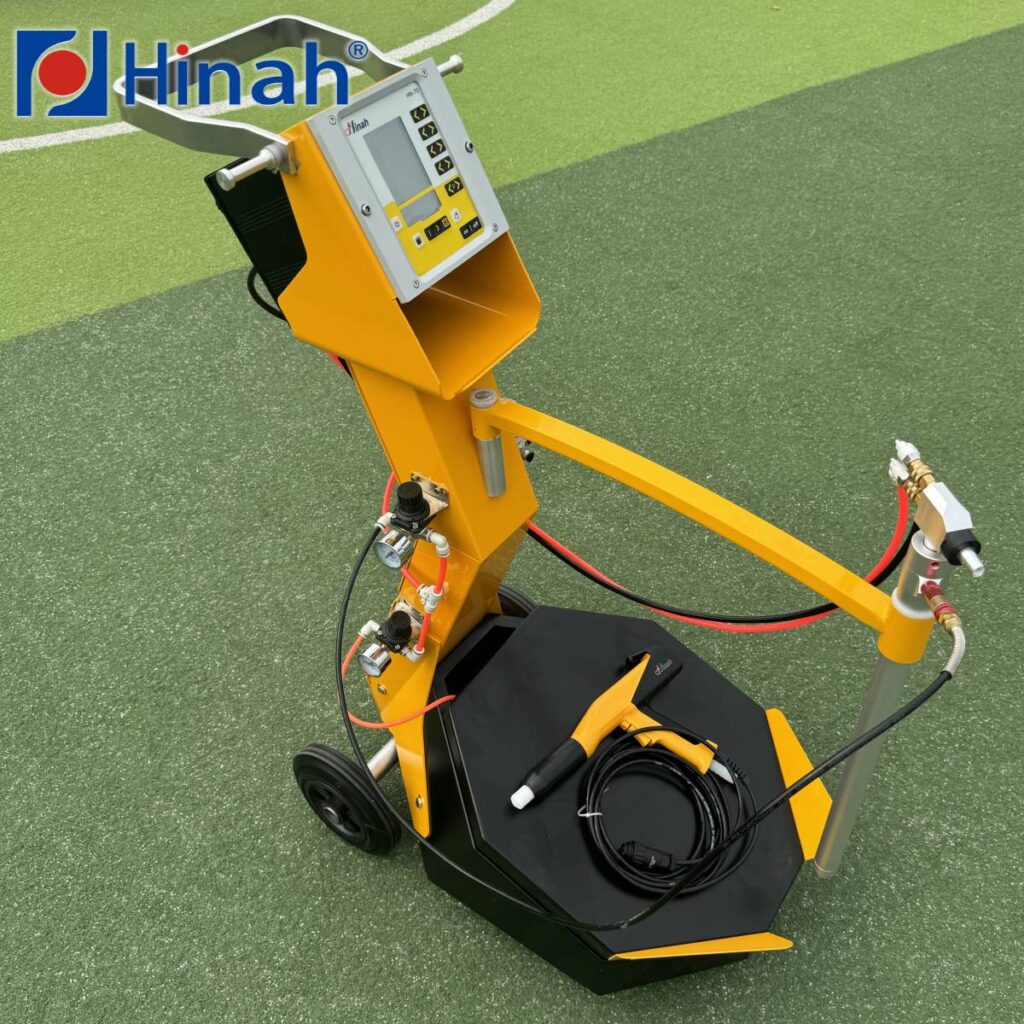
Misconception 6: ignoring the quality assurance of powder coating machine but choosing cheap equipment and
Many companies tend to choose lower-priced equipment when purchasing powder coating machines, hoping to save budget by reducing initial investment costs. However, simply pursuing low prices may ignore the quality assurance of equipment, resulting in frequent failures in the later stage, increasing additional maintenance and repair costs. Choosing a powder coating machine with a high cost-effectiveness does not mean choosing the cheapest equipment, but finding equipment with excellent quality, reliable performance and perfect after-sales service within the budget.
Misconception 7: Ignoring after-sales service and support for powder coating machine
The quality of equipment is not the only factor that affects production efficiency. Timely and professional after-sales service is also the key to ensuring the normal operation of equipment. As a high-precision equipment, powder coating machines are bound to encounter failures or maintenance needs. Without strong after-sales support, companies may face long downtime, production lines cannot operate normally, and overall operations are affected. Good after-sales service can provide timely technical support and spare parts supply when equipment problems occur, minimize downtime, and ensure the continuity of the production process.