Comprehensive Guide to Powder Coating Equipment
Powder coating, as an eco-friendly and efficient surface finishing method, relies on specialized equipment to achieve high-quality, durable coatings. This guide breaks down the key components of powder coating equipment, including pretreatment systems, spray booths, curing ovens, and auxiliary technologies. Whether you’re new to powder coating or seeking to optimize your production line, this overview will help you understand how these systems work together seamlessly.
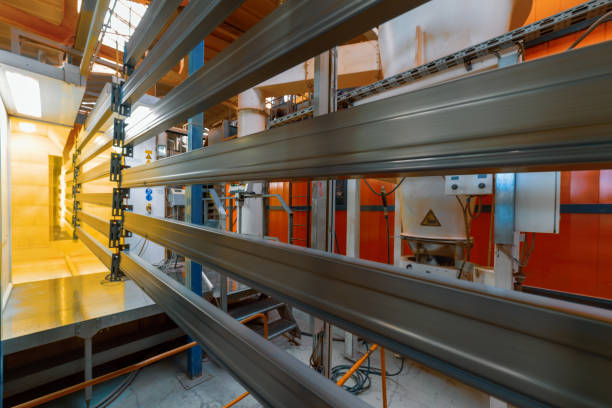
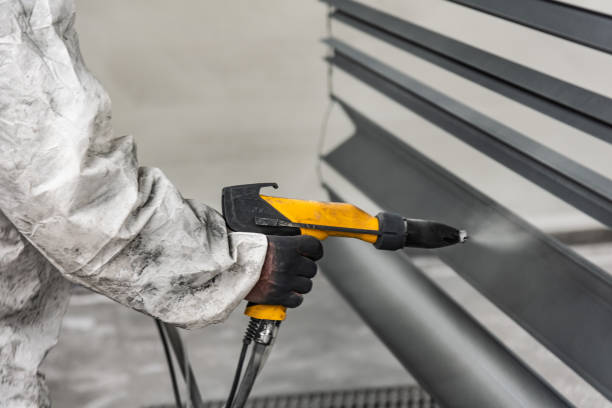
Core Components of Powder Coating Equipment
Achieving a durable and high-quality powder-coated finish requires a well-integrated system of specialized equipment. Below, we break down the essential components that make up a complete powder coating setup.
Pretreatment Equipment
Proper surface preparation is the foundation of effective powder coating. Pretreatment systems remove contaminants, enhance corrosion resistance, and ensure strong adhesion between the substrate and coating.
- Degreasing/Washing Machines
Eliminate oils, grease, and surface impurities to create a clean base for coating. These systems use alkaline or solvent-based solutions, depending on the material and contamination level.
- Phosphating/Passivation Tanks
Improve corrosion resistance and promote coating adhesion by chemically modifying the surface. Zinc and iron phosphate treatments are commonly used for metal substrates.
- Rinsing Units
Neutralize chemical residues from prior treatment steps, preventing unwanted reactions that could impact coating performance. Multiple rinsing stages ensure thorough cleaning.
- Drying Ovens
Preheat workpieces and remove residual moisture, ensuring they are ready for electrostatic powder application.
Powder Coating Systems
The core of the powder coating process involves electrostatic powder coating, where fine powder particles adhere to the substrate through an electric charge. Key equipment includes:
- Powder Coating Guns
Available in manual or automatic versions, these guns use either corona or tribo charging technology to charge and propel powder particles onto the workpiece.
- Powder Coating Booths
Designed to contain and control overspray, these enclosed workspaces feature integrated filtration and recovery systems to maximize efficiency and minimize powder loss.
– Powder Feed Centers – Regulate the supply of powder and airflow to ensure uniform application, often including fluidized beds for consistent powder flow.
Powder Coating Curing Ovens
Once the powder is applied, curing ovens melt and fuse the powder into a smooth, durable coating. Different types of curing ovens cater to specific production needs:
- Gas/Electric Convection Ovens
Use heated air circulation to evenly cure coated parts, making them ideal for large-scale operations.
- Infrared (IR) Curing Systems
Deliver rapid, energy-efficient heating by directly transferring heat to the coated surface, reducing overall curing time.
Auxiliary Systems
To improve production efficiency and quality control, powder coating lines often incorporate additional systems:
- Powder Recovery Systems
Capture and recycle excess powder, significantly reducing material waste and ensuring cost-effective operation.
- Powder Coating Conveyor Systems
Transport parts through each stage of the coating process, with options including overhead conveyor lines, power-and-free systems, and belt conveyors for various production scales.
- Control Panels
Equipped with PLC (Programmable Logic Controller) or HMI (Human-Machine Interface)** technology, these panels allow precise process monitoring and automation, ensuring consistency and reducing human error.
A well-structured powder coating system integrates all these components seamlessly, maximizing productivity while maintaining high-quality finishes.
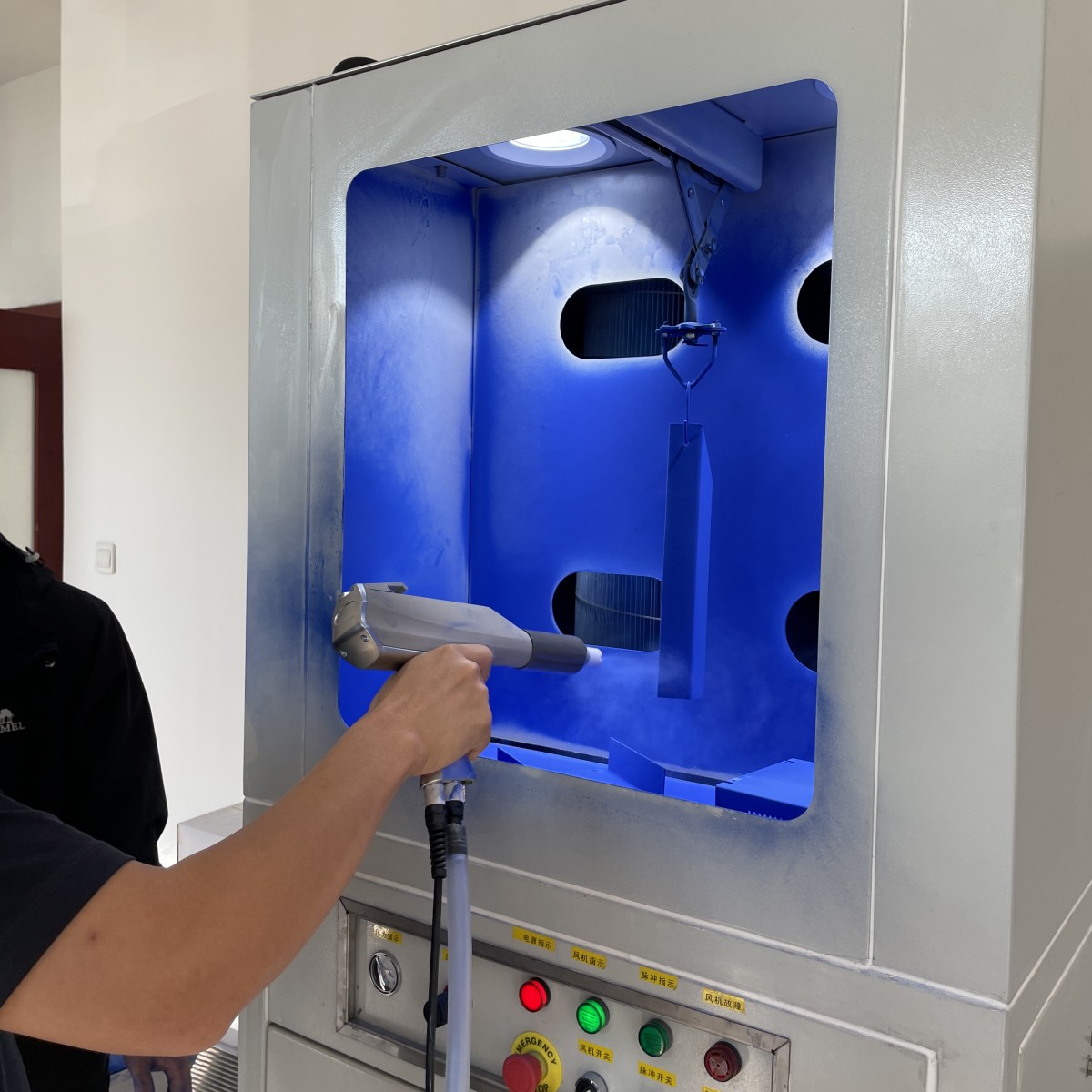
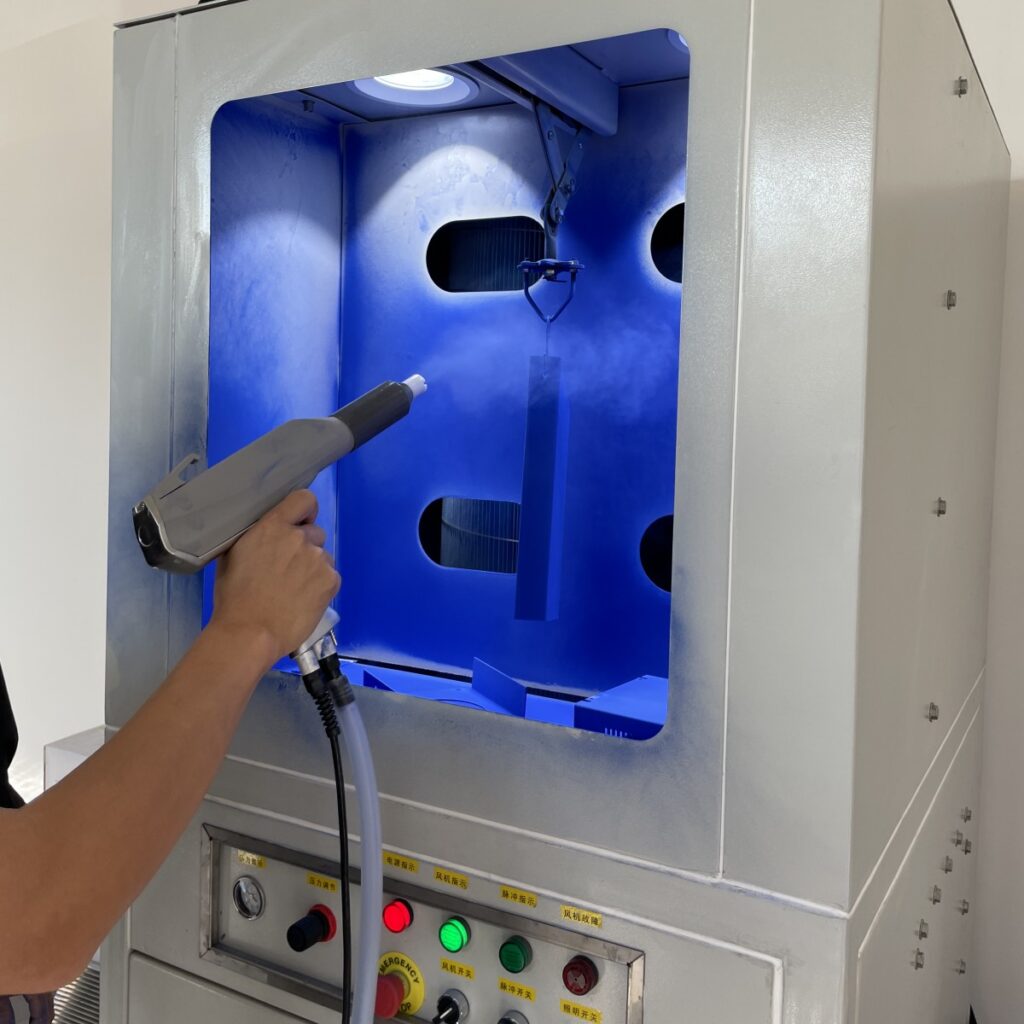
The Powder Coating Process Flow
The powder coating process includes several key steps to ensure a uniform and durable coating. First, workpiece preparation is the basis, and surface contaminants such as oil, rust and dust need to be removed by mechanical or chemical methods. Then it enters the pretreatment stage, and the adhesion and corrosion resistance of the coating are enhanced by chemical treatments such as degreasing, phosphating or passivation, and the surface is clean and free of residue after rinsing and drying. Next is electrostatic spraying, using an electrostatic spray gun to evenly adsorb the charged powder on the surface of the workpiece. After spraying, the workpiece enters the curing oven, where the powder melts and cross-links into a solid coating at high temperature. Common curing methods include hot air convection ovens and infrared curing systems. Finally, the workpiece undergoes cooling and quality inspection to ensure that the coating is uniform, firmly adhered and free of defects. If necessary, thickness, adhesion and impact resistance tests are performed to ensure the quality of the final product.
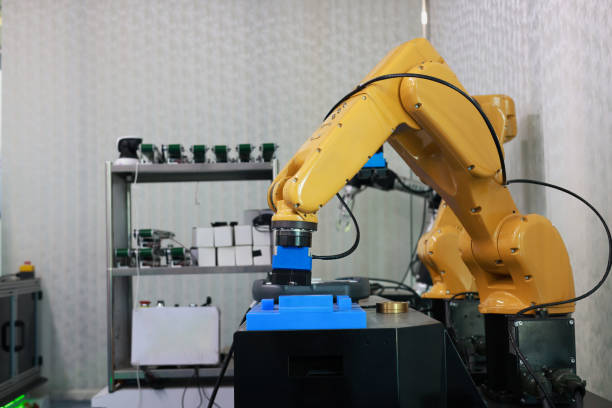

How to Select the Right Powder Coating Equipment?
Selecting the right powder coating equipment is crucial for optimizing production efficiency, ensuring high-quality finishes, and meeting sustainability goals. Here are key factors to consider when making your choice:
- By Production Scale: Tailoring Equipment to Your Needs
– Small Workshops: For businesses with lower production volumes or limited space, manual spray guns and compact curing ovens are ideal. These systems are more affordable, flexible, and suitable for smaller batches or custom work.
– Fully Automated Powder Coating Line: Large-scale operations or mass production facilities benefit from fully automated powder coating lines. These systems typically include automatic powder coating guns, conveyor systems, and advanced curing ovens, designed to handle high throughput efficiently and consistently. Automation reduces labor costs, increases productivity, and improves coating uniformity.
- By Material & Geometry: Compatibility with Various Substrates
Different materials and part shapes require specific equipment configurations to ensure optimal coating adhesion and finish quality.
– Metals: Standard powder coating equipment is generally compatible with a wide range of metals, including steel, aluminum, and galvanized surfaces. Specialized systems may be needed for materials like aluminum extrusions to ensure proper adhesion and curing.
– Plastics: Coating plastics requires equipment that can accommodate the lower thermal conductivity of these materials. Pre-treatment and curing parameters may need to be adjusted to prevent warping or distortion during the coating process.
– Complex-Shaped Parts: For parts with intricate geometries or uneven surfaces, rotating spray systems or multiple spray booths might be necessary to achieve uniform coverage. These systems ensure that every surface, regardless of shape, is evenly coated.
- By Sustainability Goals: Focusing on Efficiency and Environmental Impact
With increasing emphasis on sustainability, selecting equipment that minimizes environmental impact is becoming a priority for many manufacturers.
– High-Efficiency Recovery Rates: Powder recovery systems are critical for reducing material waste. Look for systems with closed-loop recovery to collect and reuse overspray powder, thereby minimizing waste and lowering material costs.
– Low VOC Emissions: Choose equipment that meets environmental regulations for volatile organic compounds (VOC) emissions. Advanced curing ovens and recovery systems help reduce VOCs, improving the overall environmental footprint of your operations.
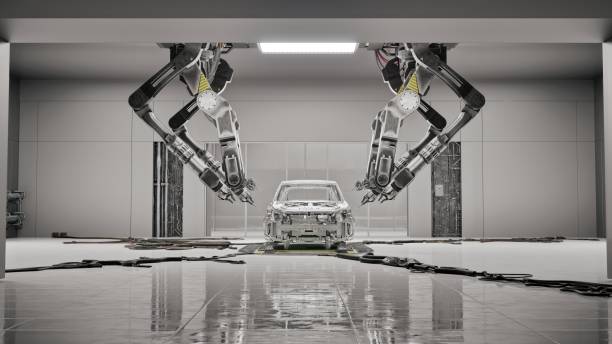
Conclusion
A well-designed powder coating system is essential for maximizing production efficiency, ensuring superior quality finishes, and meeting sustainability goals. By carefully selecting the right equipment based on your production scale, material requirements, and environmental considerations, you can optimize your coating process for long-term success.
If you’re looking to enhance your powder coating operations, our engineering team is here to help. With over 20 years of industry experience, we offer tailored solutions that are specifically designed to meet your unique needs. Contact us today to start customizing the perfect powder coating system for your business.