Why Powder Coatings Outperform Liquid Paint: 35% Cost Savings Proven
The global powder coatings market is projected to grow at 6.5% annually through 2030 (Grand View Research), driven by manufacturers seeking to slash costs and comply with tightening environmental regulations. Yet many operations still rely on liquid paint systems – a choice that quietly drains budgets through material waste, VOC emission fines, and costly reworks due to premature coating failures.
This is why forward-thinking industries from automotive to aerospace are making the strategic pivot. Powder coatings eliminate solvent use entirely, achieving over 95% material utilization rates compared to liquid paint’s 40-60% waste-heavy process.
The transition isn’t just about compliance – it’s a profitability breakthrough. As we dissect the 35% cost-saving mechanics in the next section, you’ll discover why powder coatings are redefining modern manufacturing economics.
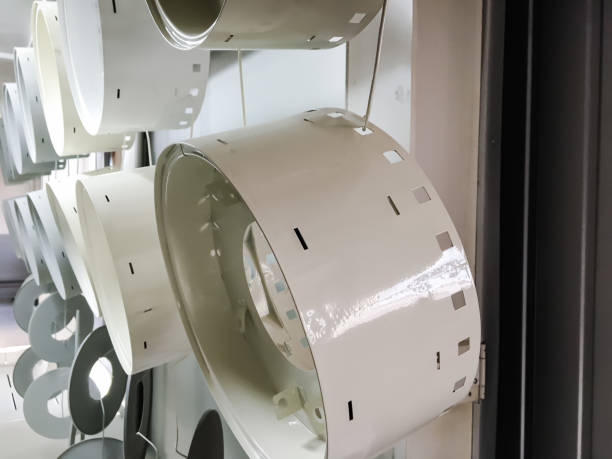
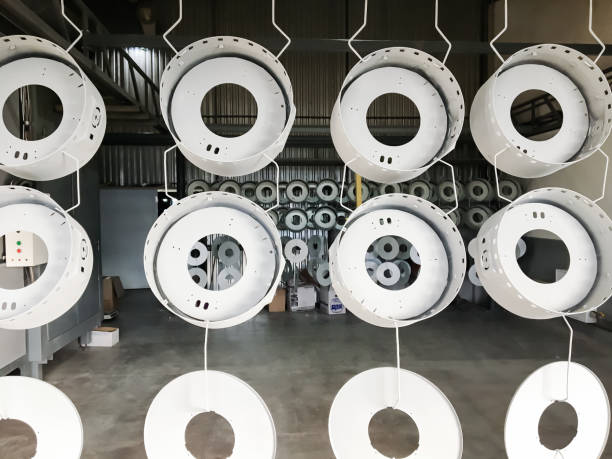
Cost Breakdown: How Powder Coatings Save 35%
The 35% cost advantage of powders isn’t a marketing claim – it’s a calculable outcome of three core efficiency pillars. Let’s dissect the numbers.
Material Efficiency
Powder coatings operate on an electrostatic application principle, where charged particles adhere almost entirely to the target surface. Industry data confirms 95%+ material utilization rates, with overspray immediately recyclable through closed-loop systems.
While liquid paint usually gets 40-60% material loss from overspray and solvent evaporation.
This efficiency directly cuts raw material procurement costs while slashing hazardous waste disposal fees by up to 90%.
Labor & Time Savings
Liquid paint’s multi-layer process demands:
- Solvent mixing and viscosity adjustments (15-20 mins/batch)
- 2-3 coats with drying intervals (4-8 hours total)
However, the powder coatings streamline operations:
- Single-coat coverage achieves 60-80μm thickness in one pass
- 3-minute curing with IR ovens vs 25-minute air drying
- $18/hr labor cost reduction per operator by eliminating solvent handling and cleanup
Long-Term Savings
The true cost of liquid paint reveals itself post-production: 18% of coated products require repainting within 2 years due to peeling/UV damage, and $50,000+/year will be spent by machinery OEMs on corrosion-related warranty claims.
While the powder coatings’ fused polymer layer resists:
- 2,000+ hours salt spray (ASTM B117) – double liquid paint’s performance
- Fade-free outdoor exposure for 10+ years
- 60% fewer field repairs reported by agricultural equipment users

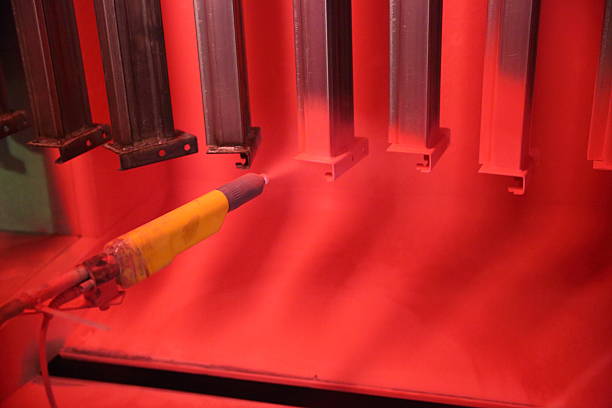
Environmental Edge: Powder Coatings as a Sustainable Choice
Powder coatings are revolutionizing sustainable manufacturing by solving liquid paint’s most pressing ecological flaw: VOC emissions. Unlike solvent-based paints that release 5-8 tons of hazardous VOCs annually per facility, powders contain no volatile organics, eliminating worker health risks.
The closed-loop system further amplifies sustainability. Over 98% of oversprayed powder is reclaimed and reused.
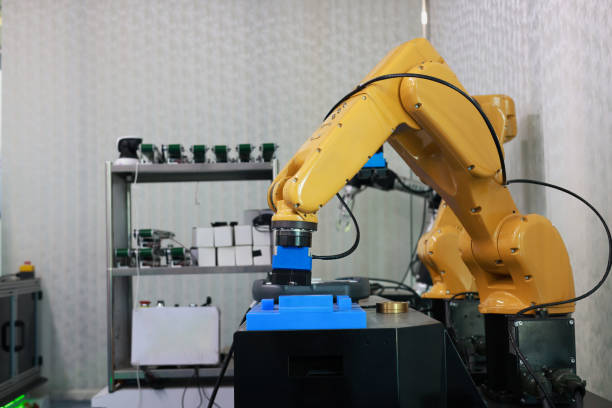
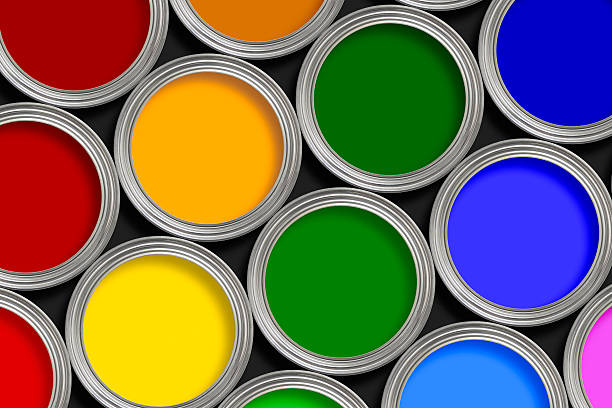
Technical Superiority of Powder Coatings
- Durability Under Stress
Powder coatings form a chemically bonded layer that outperforms liquid paint in extreme conditions. Independent ASTM B117 salt spray tests reveal powder-coated surfaces withstand 2,500+ hours without corrosion – triple the 800-hour average of liquid paint. This molecular fusion explains why Caterpillar’s coastal mining equipment shows zero rust after 15 years saltwater exposure, while the same components painted with liquid epoxy failed within 5 years.
The durability extends to physical impacts: powders achieve 5.9 ft-lb impact resistance, 60% higher than liquid alternatives, slashing shipping damage rates by 42% in Whirlpool’s appliance production. Even under relentless UV exposure, QUALICOAT-certified formulations retain 98% color stability after 5,000 hours Xenon arc testing – critical for architectural aluminum façades in desert climates like Dubai.
- Aesthetic Flexibility
Far from the limited “thick plastic” stereotype, modern powder coatings deliver sophisticated aesthetics rivaling automotive-grade liquid finishes. Through electrostatic precision, manufacturers now achieve 300+ RAL colors with metallic effects hitting ≤5GU haze levels – matching BMW’s signature liquid-painted trims. Texture innovation has unlocked everything from IKEA’s viral 2023 “Woodgrain Black” kitchen handles to anti-slip diamond patterns on Boeing aircraft stairs.
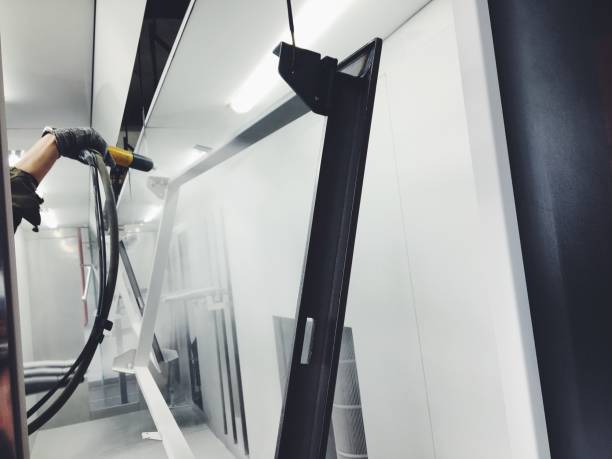
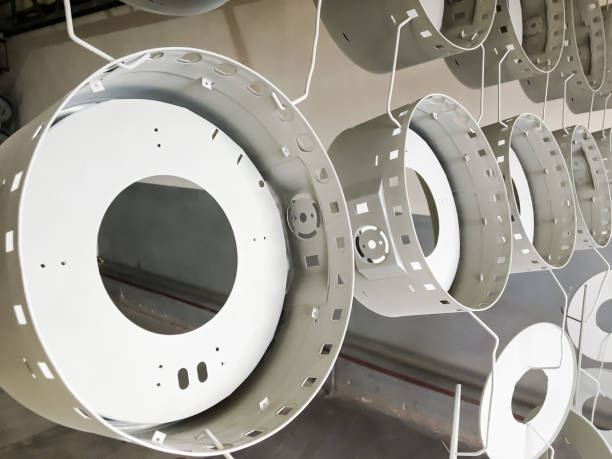
Conclusion
The evidence is irrefutable: powder coatings aren’t just an upgrade – they’re a fundamental reset for modern manufacturing. With 35% lifetime cost savings rooted in material efficiency, labor optimization, and zero-waste compliance, businesses that delay adoption risk losing ground to competitors already slashing overhead and capturing ESG-conscious markets.